Keeping abreast of current technology is a necessity. Preparing for disruptive technologies of tomorrow is expected. MCS acknowledges the potential of nanotechnology in revolutionising the future semiconductor industry landscape and is pursuing the adoption of advanced materials within the manufacture and packaging of its products.
One such material is germanene. It is made up of one-atom thick layers formed from germanium, a semiconductor that was displaced by silicon. Researchers say that electrons conduct through germanium-based material ten times faster than through silicon and five times faster than in traditional germanium. So germanene beats silicon in electron conductivity and is not susceptible to oxidation. It also beats graphene in electronic applications because it has an inherent band gap and has 60 years of characterization for the electronics industry behind it. The old adage “what goes around comes around” is now being applied in electronics: silicon may be displaced by germanene in the near future.
Graphene
Another material is graphene, the thinnest material known – it consists of a single layer of carbon atoms and is both pliable and transparent. At the same time one of the strongest – it is 300 times stronger than steel. The material conducts electricity and heat very effectively. And perhaps most importantly, it is very inexpensive to produce.
In Malaysia, the National Graphene Action Plan 2020 was drafted as a result of an extensive collaboration between the Malaysian government, private sector companies, domestic and international research institutes, and academia to assess how Malaysia can benefit from the potential of Graphene. An explicit goal of the study was to determine Malaysia’s near-term action plan when innovating with Graphene.
The NGAP2020 lays out a set of priority applications that will be beneficial to the country as a whole and what the government will do to support these efforts. One priority application is graphene-enabled conductive inks which provide a cost advantage (input and manufacturing) to radio frequency identification (RFID) applications, and eventually might be applicable to photovoltaics and printed circuits.
MCS hopes to translate its ambitions into reality and continue its legacy of creating products with leading edge technology. A prototype of the MCS e-passport with graphene antenna and MOS was showcased in the Mobile World Congress 2018 exhibition by the Italian research institute Consiglio Nazionale delle Ricerche (CNR), our technology partner. Next on our roadmap towards greener products is the technology to manufacture foldable, flexible, multi-layered printed circuit boards/layers (PCBs) made of graphene tracks on paper, plastic and other medium. And this, we believe is the next generation of electronics which will produce biodegradable products for the future.
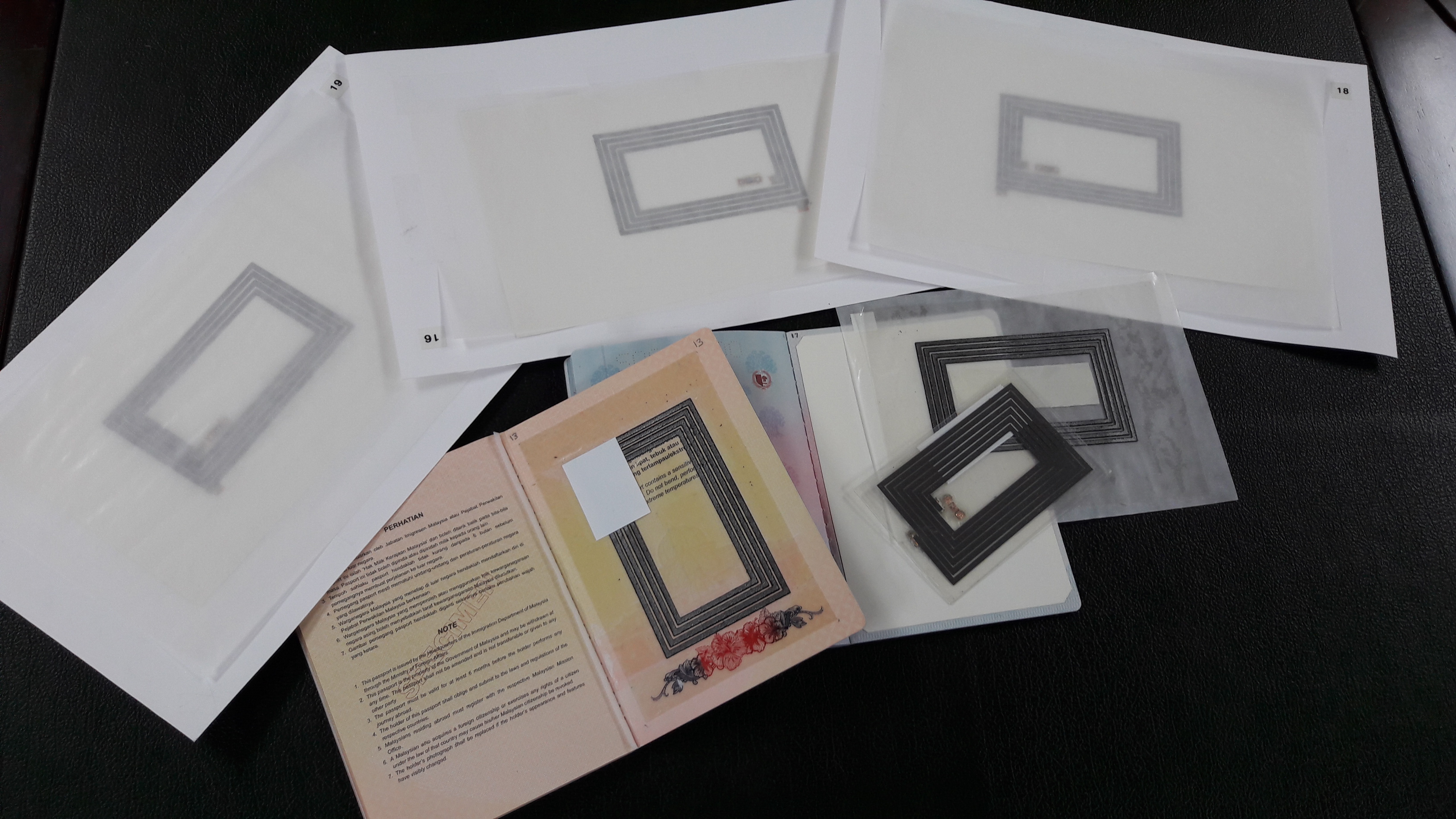